Metallhandwerk in der späten Bronzezeit
Organisation, Arbeitsaufwand und Verfahrenstechniken
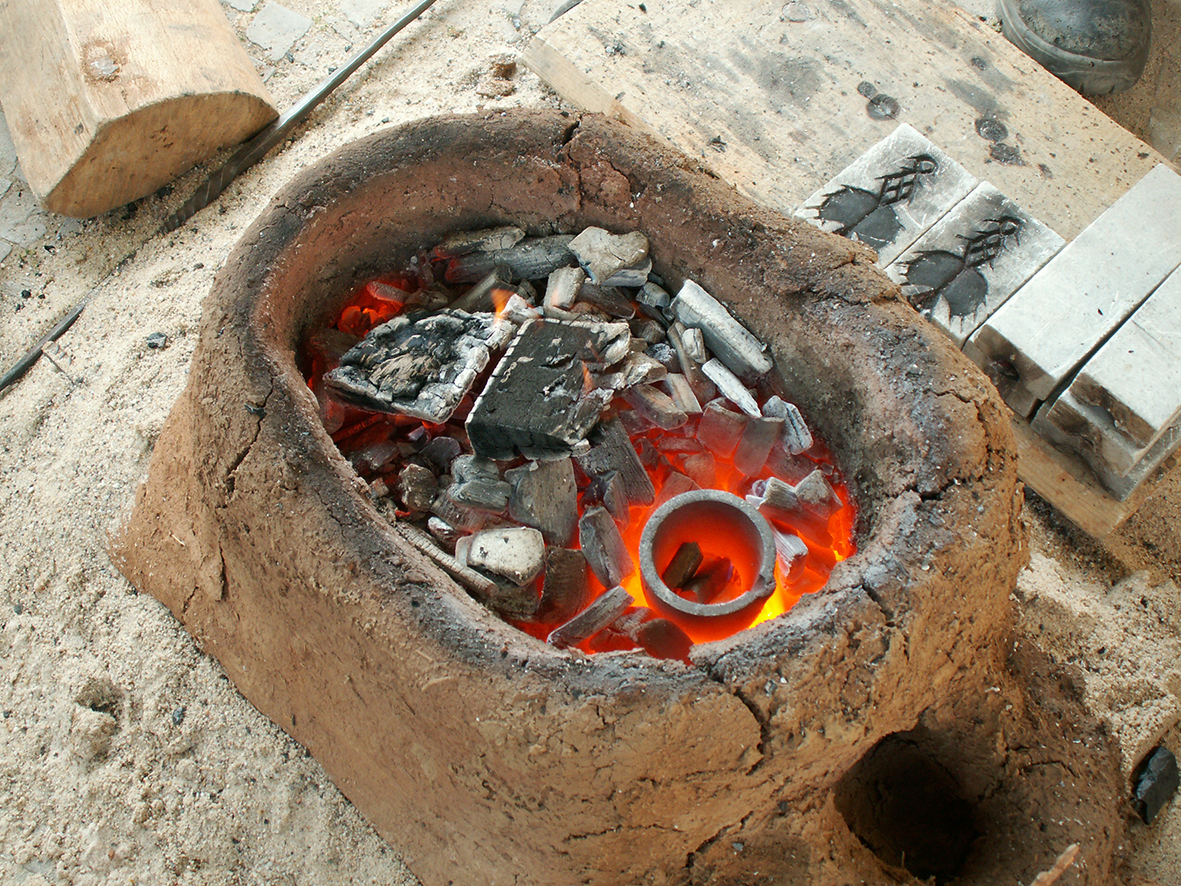
Einleitung
Untersuchungen über das bronzezeitliche Metallhandwerk sind seit geraumer Zeit ein fester Bestandteil der prähistorischen Archäologie. Soll hierbei versucht werden Organisationsabläufe, Verfahrenstechniken und Produktionsprozesse in ihrer gesamten Tiefe zu erfassen, müssen über den statischen archäologischen Bodenfund hinaus dynamische Prozessabläufe behandelt werden. Nur auf diesem Wege können Hypothesen und Modelle zielführend hinterfragt werden. Die unten aufgeführten Organisations- und Produktionsabläufe basieren auf Erfahrungen, welche die Verfasser im Laufe der Jahre mit prähistorischen Bronzebearbeitungstechniken gesammelt haben.
Unsere im Rahmen von Versuchsreihen entwickelten prähistorischen Prozessmodelle beinhalten u.a. folge Teilaspekte des Bronzehandwerks: Schmelzen der Metalle Kupfer und Zinn, systematisches Legieren dieser beiden Metalle für ein gezieltes und funktionsorientiertes Einsetzen des Werkstoffes Bronze, gießen in Stein- und Bronzeformen sowie im Wachsausschmelzverfahren, Dehnen und Strecken der Bronzeobjekte, kalt schmiedend Verdichten, Anbringen von Motiven mittels Tauschierplattierung, Gravierung und Punzierung, Durchlochung sowie Oberflächenbehandlung durch schleifen und polieren. Hier werden Produktionsschritte dargestellt, die in einem Fertigungsmodelle bei der Herstellung eines spätbronzezeitlichen Griffangelmessers anfallen.
Der hier behandelte Produktionsverlauf beinhaltet folgende Arbeitsschritte:
- schmelzen der Bronze;
- gießen der Rohform;
- abschroten und entgraten der Rohform;
- ausschmieden des Schneiden- und Angelbereichs (strecken, kalt schmiedend verdichten);
- einmeißeln der Schäftungshilfe im Griffangelbereich;
- schleifen und polieren der Oberfläche;
- verzieren durch punzieren;
- abschließendes polieren;
- schärfen des Schneidenbereichs.
Die Verfasser vertreten die Auffassung, dass die überlieferten Funde und Befunde aus dem Kontext des bronzezeitlichen Metallhandwerks eine Spezialisierung auf diesen Fertigungsbereich belegen. Die Produktion selbst eines einfachen Objektes, wie ihn die hier behandelten Messerklinge darstellt, erfordert eine detaillierte Materialkenntnis verschiedener Bronzelegierungen, ihrer unterschiedlichen Schmelzgrade und Materialeigenschaften. Hierneben sind weitere Kenntnisse, z.B. zu den Prozessen des Härtens durch kaltes Überschmieden sowie zum Punzieren vorauszusetzen. Über dieses Wissen und die entsprechenden handwerklichen Fähigkeiten musste mindestens eine der am Gesamtprozess beteiligten Personen verfügt haben.
Gussvorbereitung
Zu den gussvorbereitenden Tätigkeiten zählen die Verfasser die Organisation der Rohmaterialien und den Bau von Ofen, Gussform, Schmelztiegel und Holzzangen. Darüber hinaus müssen für die Durchführung unseres Fertigungsmodells diverse Hölzer, z.B. als Gusstiegeldeckel, Holzkohlen für die Befeuerung des Ofens sowie Feuerholz für das Ausglühen des Messerrohlings organisiert werden. Die hierfür benötigten Rohmaterialien dürften auch in der Bronzezeit allgemein zugänglich und somit unproblematisch zu beschaffen gewesen sein (Tab.01).
Lehm und Magerungsmittel werden für den Aufbau des Schmelzofens und der Tiegel benötigt. Ihre Lagerstätten sind nicht allgemein zugänglich, bzw. geeignete Materialien geographisch nicht gleichmäßig verteilt. Hier besteht eine geringe lokale Abhängigkeit von diesen Rohstoffen (Tab.01). Die Verfasser gehen davon aus, dass der Standort einer bronzezeitlichen Gießerwerkstatt diesen Bedarf berücksichtigte um "wenig wertvolle" Rohmaterialien (z.B. Lehm für einen Ofen) nicht über weitere Strecken transportieren zu müssen.
Logistisch vielschichtiger war die Versorgung mit den Metallen und mit geeignetem Rohmaterial für die in diesem Kontext verwendeten steinerne Gussformen (Tab.01). Die Lagerstätten dieser Produktionsmittel sind geographisch begrenzt und ihre Förderungs- bzw. Verhüttungsvorgänge aufwendig. Dass bronzezeitliche Werkstätten in ein weitreichendes Kommunikations- und Versorgungsnetz eingebunden gewesen sein müssen, ergibt sich alleine aus der geographischen Verteilung der Erzlagerstätten, aus denen die benötigten Metalle Zinn und Kupfer stammten. Gerade für diese beiden Materialien dürfte der organisatorische Aufwand in erster Linie an politische Abhängigkeiten gekoppelt gewesen sein. Somit ist anzunehmen, dass analog zu den heutigen Lebensumständen, zu unterschiedlichen Zeiten unterschiedliche Bedingungen bestanden. Einen wesentlichen Faktor spielte hierbei, ganz entsprechend der heutigen Situation, die Verkehrslage, in welcher sich eine Werkstatt oder ein Werkplatz befand.
Metall konnte in jeder Größe und Form bezogen werden, wobei es keine Rolle spielte, ob neu legiert oder Altware von bekannter Zusammensetzung eingeschmolzen wurde. Letztendlich musste die benötige Masse der Gussschmelze in der benötigten Qualität vorliegen. Anders verhält es sich mit dem hier verwendeten steinernen Formenmaterial, dessen Maße und dessen Form in einem direkten Bezug zum zu gießenden Objekt stehen und welches in Abhängigkeit hiervon zu organisieren war.
Abb.01 LehmofenDie Autoren verwenden in der Regel einfache schüsselförmige Lehmöfen von etwa 50 cm Länge, 40 cm Breite und 30 cm Höhe, mit auf Bodenniveau angebrachten Belüftungsöffnungen (Abb.01). Hierbei orientierten sie sich an einer ägyptischen Grabreliefdarstellung des 15. Jh. v. Chr.. Bereits an anderer Stelle wurde darauf hingewiesen, dass nach dem Auflassen eines derartigen Schmelzofens nur seine verschlackten Bereiche den Witterungsbedingungen standhalten. Die Überlieferungschancen eines bronzezeitlichen Schmelzofens der oben skizzierten Bauart, noch dazu in einem interpretierbaren Erhaltungszustand, sind somit äußerst gering.
Aufgrund eigener Erfahrungen gehen die Verfasser davon aus, dass die nicht durchgeglühten Bereiche eines derartigen prähistorischen Öfens beim Bau neuer Schmelzanlagen recycelt, bzw. gebrannte Zonen als Schamott-Zusatz für Gussformen und Gusstiegel verwendet wurden. Um für den dargestellten Schmelzofen ein Lehm-Magerungsmittel-Gemisch mit der benötigten Masse von ca. 35 kg aufzubereiten, werden etwa drei Personenarbeitsstunden benötigt. Hierauf folgt das Aufbauen des Ofens, welches ca. eine Personenarbeitsstunde in Anspruch nimmt (Tab.02).
Abb.02 SchlauchgebläseEin Belüftungssystem mit Knickdüsen (Abb.02), wie sie aus verschiedenen früh- und spätbronzezeitlichen Fundzusammenhängen belegt sind, wurden bereits an anderer Stelle behandelt. Für unsere Prozessanalysen verzichten wir in der Regel auf den Einsatz eines Schlauchgebläses (Abb.02) und ersetzten das am Boden liegenden Topfgebläse der oben genannten ägyptischen Darstellung aus Gründen der Durchführbarkeit - es steht zur Bedienung des Gebläses in der Regel nur eine Person zur Verfügung - durch zwei Belüftungssysteme nach antikem Vorbild (Abb.01), mit dem bei maximalem Auszug ein Luftfassungsvermögen von etwa 22,5 l pro Balg erreicht wird. Der Aufbau, mit der Verbindung dieses Belüftungssystems mit dem Ofen, nimmt etwa 0,5 h in Anspruch (Tab.02).
Bei dem verwendeten Brennmaterial steht für uns die optimale Ausnutzung der verfügbaren Energieressourcen im Vordergrund. Auch wenn in Versuchsreihen bereits das Schmelzen von Bronze mit Feuerholz bei Temperaturen von 1170 °C gelungen ist, verwenden wir bei unseren Versuchsreihen ausschließlich Holzkohlen. Hierbei gehen wir davon aus, dass der höhere Brennwert der Holzkohle bekannt war. Gezieltes Experimentieren mit Holzkohlen verschiedener Baumarten und unterschiedlicher Größen führten zu einer Optimierung des oben beschriebenen Ofensystems. Hierbei erwies sich Buchenholzkohle mit einer Stückgröße von 4-6 cm als besonders geeignet, da sie die Parameter 'Luftzirkulation' und 'Temperaturkonzentration', welche den Wirkungsgrad maßgeblich bestimmen, in das beste Verhältnis setzt. Um eine gussfähige Bronzespeise von etwa 0,1 kg Masse zu erzielen, wie sie für den hier behandelten Guss benötigt wird, verbrauchen wir etwa 3-4 kg dieser Buchenholzkohle (Tab.01).
Bereits die kupferzeitliche Schmelztiegel der Pfyner Kultur weisen verhältnismäßig größere Volumen auf (125 cm3, Schreckensee, Kr. Ravensburg, BRD, 135 cm3, Bodmann, Kr. Konstanz, BRD). Unsere Versuche konnten zeigten, dass das Volumen eines derartigen Schmelztiegels nicht komplett ausgenutzt werden kann, da ein sicheres Ausgießen des randvollen Tiegels nicht möglich ist, bzw. seine Handhabung mit einfachen Werkzeugen, z.B. Holzzangen und / oder Holzgriffen dies nicht zulässt. Schmelz- und Gießversuche verdeutlichten, dass Gusstiegel maximal bis etwa zu ¾ ihrer Höhe gefüllt werden sollten. Der von uns für die hier benötigte kleine Gussspeisenmasse verwendete Schmelztiegel weist ein Volumen von 140 cm³ auf. Er wird aus etwa 1 kg Lehm-Magerungsgemisch hergestellt (Tab.01).
Die Tiegelform scheint beim prähistorischen Bronzeguss keinen bestimmenden Faktor dargestellt zu haben. So differenziert z.B. J. Waldhauser für Böhmen und Mähren fünf Tiegeltypen, die er für den Zeitraum Ha D - Lt D1 eher chronologisch als funktional interpretiert. Für das Aufbauen eines Gusstiegels mit Materialvorbereitung und Ausformen des Tiegels ist knapp eine Personenarbeitsstunde zu veranschlagen. Der Bau einer Holzzange zur Handhabung des Gusstiegels erfordert wiederum etwa eine Personenarbeitsstunde (Tab.02).
Mittig verlaufende Gussnähte an Bronzefunden der frühen Bronzezeit belegen, dass die Technologie des Kokillengusses bereits in dieser frühen Phase der Metallverarbeitung bekannt war. Die Kokillentechnik hat den Vorteil, dass größere Lunker in der Regel im abzutrennenden oberen Eingussbereich des Gusszapfens liegen, im deutlichen Unterschied zum Verfahren des verdeckten Herdgusses, bei dem das Negativ in nur eine Formenhälfte eingearbeitet ist und mit der anderen Formhälfte, die glatt verbleibt, nach dem Guss abgedeckt oder abgezogen wird. Hierbei treten Lunker ungleichmäßig verteilt im gesamten Bronzeobjekt auf.
Gegenüber dem oft unreflektiert angenommenen Guss in einer offenen Form (offener Herdguss), bei welchem die Gussspeise in eine Form gegossen wird, welche nicht abgedeckt worden sein soll, liegt ein weiterer und entscheidender Vorteil der Kokillenmethode darin, dass glatte Oberflächen ohne störende Oxydschichten entstehen. In offenen Formen bildet sich an der dem Sauerstoff ausgesetzten Seite des Gusses eine Oxydschicht mit rauer "milchhautartiger" Oberfläche (s.: ebd., Abb.4). Diese Oxydschicht kann deutliche Fehlstellen und Unreinheiten hervorrufen, wenn sie in ein Werkstück hineingearbeitet würde. Aus diesem Grunde müsste sie vor einem Ausschmieden oder Verzieren entfernt werden, was einen unnötigen zusätzlichen Arbeitsaufwand durch Schleifen bedeutet.
Abb.03 Zinnbronze
Abb.04 steinerne GussformGussformen aus Sandstein, Speckstein, Glimmerschiefer und anderen Gesteinen sind in Europa nachweislich vom ausgehenden Neolithikum an bis in die historischen Perioden benutzt worden. Erfahrungsgemäß sollte die Beständigkeit des Gussformenmaterials, insbesonders für Fertigungsprozesse von reinen Gebrauchsgegenständen ("Massenprodukten"), ein maßgeblichen Faktor bei der Auswahl dieses Materials sein (vgl.: ebd.). Ihm gegenüber spielt der Arbeitsaufwand, welcher nötig ist um die gewünschte Form herzustellen, eine eher untergeordnete Rolle. Immer vorausgesetzt durch das ausgesuchte Formenmaterial ist eine bestimmte Gussleistung und Produktqualität gewährleistet. Insbesondere die in diesem Formenmaterial beim Rohstück erzeugte Oberflächenbeschaffenheit steuert in der Folge den Aufwand der weiteren Bearbeitungsschritte. Raue und unebene Oberflächen bedeuten einen höheren Arbeitsaufwand. Auf diesen Überlegungen aufbauend verwenden wir für unsere Formen Varietäten spezieller Speck- oder Sandsteine, Materialien welche nachweislich auch im prähistorischen und antiken Metallhandwerk Verwendung fanden. Diese Materialien sind besonders standfest und gewährleistet in der Regel plane Oberflächen. Das "Aufsägen" des Formenrohmaterials mit einer "Bronzesäge" und anschließendem Planschleifen der Innenseiten (1,5 h), bzw. wahlweise das Brechen, Picken und Planschleifen des Formenrohmaterials (2 h) sowie das zweiseitige Ausarbeiten des Formennegativs (2X40 min) mit Anlage der vier Bohrungen für die zwei Fixierstifte (45 min), erfordern unter ausschließlicher Verwendung bronzezeitlicher Werkzeuge ( 8% Zinnbronze) (Abb.03) sowie weiterer natürlicher Hilfsmittel (z.B. Sandstein als Schleifmittel) etwa 3,5 h bzw. 4 h Personenarbeitsstunden (Tab.02). Bei der Verwendung von Speckstein wird hierbei eine Form mit einer Masse von etwa 2,2 kg hergestellt (Tab.01). Insgesamt benötigen somit die gussvorbereitenden Tätigkeiten unter Verwendung einer steinernen Gussform (Abb.04) etwa 10,5 bzw. 10 Personenarbeitsstunden (Tab.02).
Die Verfasser haben die Erfahrung, dass die Werkzeuge eines bronzezeitlichen Metallhandwerkers so gestaltet sein mussten, dass eine direkte Impulsübertragung vom Werkzeug zum bearbeiteten Werkstück, ohne ein dämpfendes Zwischenstück, gewährleistet ist. Nur so stehen bei der Bronzebearbeitung der erforderliche Kraftaufwand und die sichere Führung des Geräts in einem funktionalen Verhältnis. Werkzeuge mit Randleisten, Tüllen o. ä. Hinweise auf Schäftungen sind außerhalb der Metallbearbeitung benutzt worden, z.B. als Beitel in der Holzverarbeitung.
Aus der späten Bronzezeit sind eindeutige Ambosse, Hämmer, Meißel, Stichel und Punzen überliefert. Depots wie der Befund von Génelard (Saône-et-Loire, Frankreich) und Einzelfunde belegen für diese Phase der Bronzezeit eine Vielzahl an speziellen Werkzeugen, darunter auch ein Amboss aus der Schweiz (Wollishofen, Kt. Zürich), den die Verfasser als Vorbild für ihren Bronzeamboss (8% Zinnbronze) auswählten (Abb.06). Mit Bezugnahme auf seine eigenen Versuchsreihen schlug H. Drescher zur Anfertigung von Punzen Bronzen mit einem Zinngehalt von 6-15 % vor, deren Schneiden durch Hämmern gehärtet und dann nachgeschliffen wurden. Die Bandbreite der Mischungsverhältnisse unserer Punzen-, Stichel- und Meißelbronzen (z.B. Abb.03) liegt in der Regel zwischen 8-17 % Zinn und 83-92 % Kupfer. Unterschreiten wir beim zugefügten Zinn diesen Varianzbereich, so verlieren die Schneiden der oben genannten Werkzeuge sehr schnell an Standzeit, überschreiten wir ihn, werden die Schneidenbereiche deutlich spröder. Dieses erhöht wiederum die Gefahr eines ausbrechenden Schneidenbereichs.
Die Verwendung reiner Zinnbronzen mit einem Zinngehalt von über 8-15 % ist nicht unproblematisch. Diese Bronzen neigen bei ihrem Erstarren zu starken Seigerungserscheinungen. Um diesen Zustand wieder auszugleichen, d.h. eine erneute "Homogenisierung" der Bronzelegierung herbeizuführen, müssen Werkstücke, die einer starken Kaltumformung unterliegen, über einen gewissen Zeitraum Temperaturen über 550 °C ausgesetzt werden. Hierdurch wird ein gleichmäßigeres Gefüge der Substitutionsmischkristalle erreicht. Die Werkstoffeigenschaften werden optimiert. Ohne diesen Prozess neigen Bronzen mit starken Seigerungen bei der notwendigen Kaltverfestigung (s.u.) oder spätestens bei ihrer Verwendung verstärkt zum Bruch. In unseren Versuchsreihen werden die Meißel, Punzen und Stichel nach dem Guss zuerst überschliffen und danach die Schneidebereiche vor dem Schärfen kalt schmiedend verfestigt. Hierbei bewirkt die Kaltverformung der Kupfer-Zinnbronzen, durch eine Veränderungen der Metallstruktur, günstigere Materialeigenschaften.
Der Guss
Zum Vorheizen des Ofens ist ein Zeitaufwand von etwa 45 min bis max. einer Stunde notwendig. Hierbei entsteht ein gleichmäßig durchgeglühtes Holzkohlebett. Der darin eingebettete Schmelztiegel, mit dem noch kalten Rohmaterial, erreicht langsam und selbstständig eine Ausgangstemperatur von 600-700 °C. Parallel hierzu wird die Gussform von einer Person vorbereitet. Insgesamt werden hierfür etwa 15 min reine Arbeitszeit benötigt (Tab.03). Gleichzeitig erfolgt das Hochfahren der Temperatur des Gussofens, bis die Gussspeise etwa 1150°C erreicht hat. Hierbei steckt die wesentliche Arbeitsleistung in der Belüftung des Schmelzofens, für welche bei einem Betrieb mit einem Blasebalg nach antikem Vorbild (Abb.01) eine Person notwendig ist. Die gewünschte Gusstemperatur ist nach etwa 15 Minuten erreicht. Eine zweite Person betreut den Gusstiegel, bis dieser aus der Glut genommen werden kann, um die flüssige Gussspeise in die Form zu gießen. Für diesen sehr schnell ablaufenden Produktionsschritt sind zwei Personen nötig. Insgesamt sind somit für die eigentliche Gussdurchführung mit einem antiken Belüftungssystem etwa ¾ Personenarbeitsstunden zu veranschlagen (Tab.03).
In diesem Fertigungsmodell greifen wir auf bereits legierte Zinnbronze (8% Zinnanteil) zurück. Hierbei orientieren wir uns an den zahlreichen Hack-Bronze-Depots die eine Wiederverwertung von unbrauchbaren Bronzegegenständen belegen und die neues Legieren nicht zwingend notwendig machen. Hierneben zeigen Depots von Bronzebarren, dass von den bronzezeitlichen Gießern auch auf standardisierte Volumen und Legierungen zurückgegriffen werden konnte. Da neben der Masse des eigentlichen Rohgusses auch die der Bronze des Gusskanals und eines möglichen Giesverlusts einkalkuliert werden muss, ist die Masse der verflüssigten Gussspeise in der Regel höher als die des produzierten Rohstückes. Im hier geschilderten Fall liegt sie bei etwa 100 g je Gussvorgang. Die im Kokillenguss produzierte Gussrohlinge weisen geringe Schwankungen in ihren Massen auf, was auf die unterschiedlichen Füllungen des Eingusskanals zurückzuführen ist. Von zehn, für diese Darstellung durchgeführten Güssen, liefen sieben Gussrohlinge gut aus, von denen fünf weiter verarbeitet wurden. Die weiterverarbeiteten Gussrohlinge (exemplarisch: Abb.04, Abb.5.1) wogen zwischen 75 g und 82 g (Tab.04).
Weiterverarbeitung
Abb.05 Messerrohlinge
Abb.06 Bronzehammer Nach dem Abschroten und Entgraten lagen Messerrohlinge (exemplarisch: Abb.5.2) mit Massen vor, die zwischen 57,0 g und 59,5 g schwankten (Tab.04). Die Rohformen schneidender Geräte weisen in der Regel einen zu dicken Schneidenbereich auf. Hieraus resultiert, dass dieser im Sinne einer modernen Sense gedengelt, d.h. ausgedünnt werden muss. Für diese Treibarbeiten verwenden wir den oben erwähnten Bronzeamboss (8% Zinngehalt) und einen Bronzehammer (5% Zinngehalt, 620g) (Abb.06). Steinhämmer im Sinne der bekannten Rillenschlägel lehnen die Verfasser nach eigenen Erfahrungen in verschiedenen Versuchsreihen für diese präzise und mit einem hohen Kraftaufwand durchgeführten Arbeiten ab. Die für die Ausschmiedevorgänge mit dem Bronzehammer aufzuwendende Arbeitszeit schwankt zwischen 27 min und 36 min (Tab.04).
Um Werkstücken, die den oben skizzierten Verformungsprozess mehrmals und intensiv durchlaufen, die bei der Kaltverformung entstehenden Spannungen nehmen zu können und ein Einreißen der Randbereiche zu verhindern, ist nach der flächigen Überarbeitung des Werkstückes das Erhitzen des Objektes auf etwa 500-700 °C und ein nachfolgendes Abschrecken des Stückes notwendig. Dieser Prozess führt zu einem erneuten "Weichwerden" des Bronzeobjektes. Ist die Klinge ausreichend ausgedünnt worden, verbleibt ihr Schneidenbereich nach dem letzten Überschmieden gehärtet. Das Ausglühen (1 X pro. Klingenrohling a 20 min) erfordert keinen zusätzlichen Arbeitsaufwand. Nach diesem Produktionsschritt wird mit dem Bronzemeißel (15% Zinngehalt) im Griffangelbereich eine Aufrauung des Kantenbereichs als Schäftungshilfe angebracht, was einen Arbeitsaufwand von etwa drei Minuten pro Klinge erfordert. Hierauf erfolgt ein letztes Informschleifen der durch das Ausschmieden gering verlaufenen Konturen, wobei die im Zuge der Treibarbeit vergrößerte Fläche erneut reduziert wird. Ein Feinschliff mit Sandstein und das Polieren der Oberfläche mit Schachtelhalm schließt die funktionale Fertigstellung der Messerklingen ab. Durchschnittlich werden hierfür weitere 20 min Arbeitszeit benötigt. Somit wird für die geschilderten Weiterverarbeitungsprozesse vom Rohguss zur funktionsfähigen Klinge (Abb.5.3) maximal eine Arbeitsstunde benötigt.
Gravierungen und Punzierungen von Zierlinien sind bereits auf Objekten der Frühbronzezeit belegen. Sie verdeutlichen schon für diese frühe Phase geographisch weit verbreitete werkzeugtechnische Kenntnisse. Orientiert an spätbronzezeitlichen Befunden brachten wir auf den Klingen gepunzte Ornamente an, die sich aus einfachen Punktreihen zusammensetzten (Arbeitsaufwand pro Klingenseite 10-15 min). Hierauf erfolgte das Schäften der Klinge in einem vorbereiteten Griff sowie das abschließende Schärfen des Schneidenbereichs, wodurch weitere 10 Minuten Arbeitszeit anfielen.
Resümee
Wir möchten nicht darüber hinwegtäuschen, dass wir nur Aspekte eines Fertigungsmodells vorgestellt haben, welches auf unseren Erfahrungen und unserem logistischen Netzwerk beruht. Die dargestellten Prozesse können somit nur an bronzezeitliche Technologien und Produktionsabläufe annähernde Möglichkeiten aufzeigen, die es durch weitere Versuchsreihen noch zu verdichten gilt. Die hier dargestellten, in der Werkstatt eines Metallhandwerkers stattfindenden Prozesse sind grob in zwei Arbeitsabläufe einzuteilen:
- Von der Rohbronze bis zum Rohguss.
- Vom Rohgusses bis zur funktionsfähigen Messerklinge.
In der ersten Stufe des Gesamtprozesses werden, in Abhängigkeit des Blasebalgsystems, drei bis vier Arbeitskräfte benötigt um einen Rohguss zu erzielen. Die an die hierbei durchgeführten Tätigkeiten gekoppelten logistischen Abhängigkeiten sind nur sehr schwer einzuschätzen. Die Verfasser gehen davon aus, dass es ausreichte, dass an einem derartigen Fertigungsprozess nur eine Person beteiligt war, die über das technische Wissen und über das benötigte logistische Netzwerk verfügte hat.
Die Weiterverarbeitung des Rohgusses bis zur funktional fertigen Messerklinge erfordert diese Fachkenntnis nicht in diesem Maße. Die Autoren nehmen an, dass die bronzezeitliche Gesellschaft bis zu einem gewissen Grad vertraut war mit dem Werkstoff Bronze und den Prozess des Kaltverformens (innerhalb gewisser Grenzen) sowie den Prozessen des Nachschärfens durch dengeln und schleifen beherrschte. Diese Fähigkeiten waren beim allgemeinen Umgang mit schneidenden Bronzewerkzeugen in der gesamten Bevölkerung permanent gefordert. Anders verhält es sich mit den Arbeitsschritten des Abschrotens und Verzierens durch Punzieren. Insbesondere letzteres ist nur mit einiger Erfahrung von einer geschulten Person durchzuführen. Darüber hinaus herrschte jedoch kein weiterer Bedarf an ausgebildeten Arbeitskräften.
Abbildungsunterschriften
Abb.01 Rekonstruierter Bronzeschmelzofen mit zwei Belüftungssystemen nach antikem Vorbild (Foto: Holdermann / Trommer 2007)
Abb.02 Rekonstruiertes bronzezeitliches Schmelzofensystem mit Knickdüse und Schlauchblasebalgen (Foto: Holdermann / Trommer 2008)
Abb.03 Bronzewerkzeuge zum Fertigen der steinernen Gussform sowie zum Abschroten des Gusszapfens, von links: Bronzemeißel (15% Zinn), 2 X Bronzemeiße (8% Zinn), 2 X Bronzestichel (8% Zinn) (Foto: Holdermann / Trommer 2008)
Abb.04 Steinerne Gussform aus Speckstein (Lmax= 18 cm, Bmax= 8 cm), mit Gussrohling (Foto: Holdermann/Trommer 2008)
Abb.05 Von oben nach unten: Im Kokillenverfahren gegossener Gussrohlinge, abgeschrotetes Werkstück, ausgeschmiedete und polierte funktionsfähige Bronzeklinge (Foto Holdermann / Trommer 2008)
Abb.06 Ausschmiedeprozess mit dem Bronzehammer auf dem Bronzeamboss (Foto: Holdermann / Trommer 2008)
Tabellen
Geschätzter Organisationsaufwand bei ausgewählten Rohstoffen
Produktionsmittel | Material | Bedarf | Ressourcenverfügbarkeit | Beschaffung |
---|---|---|---|---|
Ofen | Lehm, Magerung | 35,0 kg | geringe lokale Abhängigkeit | unproblematisch |
Gussform | Stein | >=2,2 kg (18X6X8 cm) | lokale Abhängigkeit | logistisch aufwendig |
Gusstiegel | Lehm, Magerung |
1,0 kg | geringe lokale Abhängigkeit | unproblematisch |
Zange | Holz, Rohhaut |
/ | allgemein zugänglich | unproblematisch |
Befeuerung | Holzkohle | 3-4 kg | allgemein zugänglich | unproblematisch |
Gussspeise | Bronze: Kupfer, Zinn | 0,1 kg pro. Rohguss | lokale Abhängigkeit | logistisch aufwendig |
Tab.01 Geschätzter Organisationsaufwand bei ausgewählten Rohstoffen
Arbeitsaufwand bei gussvorbereitenden Tätigkeiten
Prozess | Material | Tätigkeit | Personenarbeitsstunden | |
---|---|---|---|---|
Bau des Ofens | Lehm, Magerung 35,0 kg | Aufbereitung des Lehm-, Magerungsgemisches, Aufbau des Ofens | 4 h | |
Herstellung der Funktionsfähigkeit des Ofens | - | Verbindung des Belüftungssystems mit dem Ofen | 0,5 h | |
Bau der Gussform | Stein 2,2 kg | Spalten, Picken,Glätten und Ausarbeiten der Gussform | 4 h | |
Aufsägen, Glätten und Ausarbeiten der Gussform | 3,5 h | |||
Bau des Tiegels | Lehm, Magerung 1,0 kg | Aufbereitung des Lehm-, Magerungsgemisches, Aufbau und Brenne des Tiegels | 1 h | |
Bau der Zange | Holz/Rohhaut | Spalten des Rohlings, Schneiden eines Riemens, Verknoten | 1 h | |
Total | 10,5 h | 10 h |
Tab.02 Arbeitsaufwand bei gussvorbereitenden Tätigkeiten (ohne Anfertigung der Bronzewerkzeuge)
Arbeitsaufwand beim Guss einer Messerklinge
Prozess | Tätigkeit | Personenarbeitsstunden |
---|---|---|
Vorheizen des Ofens | Auffüllen mit Holzkohle, Anfeuern | Zeitbedarf ca. 45 - 60 min, keine Arbeitszeit |
Vorbereiten der Steinform | Präparieren der Form: Vorwärmen, Einrußen, Zusammensetzen | ca. 15 min |
Hochfahren der Temperatur in Tiegel und Gussspeise | Belüftung des Ofens, umgesetzt auf antikes System, durch eine Person, zusätzlich eine Person für Tiegelbetreuung. | 15 min X 2 Personen |
Guss des Klingenrohlings | Entnahme des Tiegels und Guss durch 2 Personen | < 1 min |
Total | ca. 45 min |
Tab.03 Arbeitsaufwand beim Guss einer Messerklinge (Masse der Gussspeise: 0,1 kg)
Masse der Gussrohlinge, Masse und Maße der abgeschroteten Stücke sowie Arbeitsaufwand des Ausschmiedens des jeweiligen Schneidenbereichs
Guss | Gossrohling (Masse) | abgeschrotet | Lmax | Bmax | Dmax | Arbeitsaufwand ausschmieden |
---|---|---|---|---|---|---|
Nr.01 | 82,0 g | 57,0 g | 15,5 cm | 2,6 cm | 0,4 mm | 27 min |
Nr.02 | 79,0 g | 58,0 g | 15,4 cm | 2,7cm | 0,4 mm | 32 min |
Nr.03 | 79,0 g | 59,5 g | 15,5 cm | 2,6 cm | 0,4 mm | 36 min |
Nr.04 | 75,0 g | 59,5 g | 15,6 cm | 2,7 cm | 0,4 mm | 28 min |
Nr.05 | 79,0 g | 57,0 g | 15,7 cm | 2,6 cm | 0,4 mm | 35 min |
Tab.04 Masse der Gussrohlinge, Masse und Maße der abgeschroteten Stücke sowie Arbeitsaufwand des Ausschmiedens des jeweiligen Schneidenbereichs